Ideal for Space-constrained and harsh environmental applications
Case 1: Wireless data acquisition technology on the shop floor
The shop floor, such as an assembly line, is where a factory’s main production takes place. Typically, production line operators require alarm buttons, component shortage buttons and other performance indicators. Linear topology is the most common design arrangement for most modern production lines.
Moxa’s ioLogik E1200, with its daisy-chain connection, is a perfect solution for a linear production line, workbench or factory floor. Customers can, furthermore, connect ioLogik with our AWK 1121 WLAN Client to provide seamless wireless communication between the control room and the shop floor.
The daisy-chain wiring technology is specially designed for linear production lines. With Moxa AWK 1121 WLAN Client, customers will not only streamline the communication process, but also reduce cabling cost and wiring efforts.
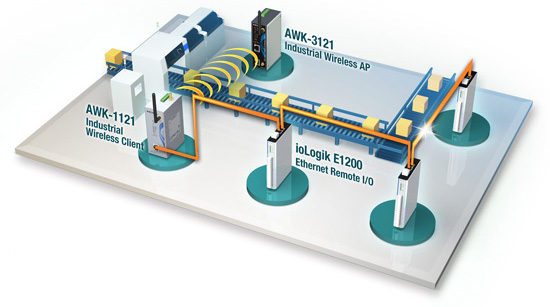
Case 2: Ethernet-based data acquisition technology in automated factories
In the modern factory, field bus and Ethernet are used simultaneously. If customers want to use Ethernet as their communication backbone, they must convert different IO signals and field bus into Ethernet.
Ethernet communication is increasingly common in automated factories, and as a result, engineers will want to connect equipment like legacy devices or I/O sensors via Ethernet. Moxa offers field bus conversion and Ethernet-based I/O. Modbus, Ethernet/IP, or Profibus are all supported in Moxa’s field bus conversion. Moxa offers cost effective Ethernet I/O to help engineers directly collect signals from sensors.
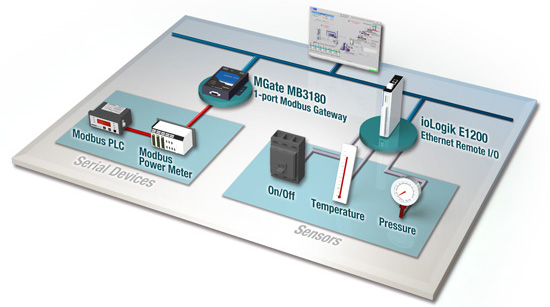
Case 3: A compact industrial-grade WLAN client for Automated Guided Vehicle Systems
With advancements in warehouse management systems, new technologies are being implemented to lower operational costs and improve efficiency within the warehouse environment. To this end,
warehouse operations are increasingly using Automated Guided
Vehicles (AGVs) to replace manually operated forklifts. In order to
operate and monitor these unmanned AGVs, Automatic ID Data
Capture technologies are set up in an intricate WLAN network.
Safely operating and monitoring an AGV requires a continuous relay of data, data that is collected by a sophisticated network of sensors and transceivers. Despite limited space, an AGV forklift must host up to 20 sensors, as well as Ethernet I/O and WLAN devices. This means that
the physical size of each component is an important factor in the system design.
The Moxa ioLogik E1200 is rugged and compact and, as such, is an ideal technology for maintaining accurate position and distance detection, as well as a responsive start/stop signal. AGVs can thus provide greater efficiency when collecting or moving various products. Customers can connect the ioLogik E1200 with the AWK 1121/1127 to provide wireless communication architecture between AGVs and the warehouse’s central command.
The AWK-1121/1127 series is a new line of IEEE 802.11 a/b/g WLAN clients. Engineered with industrial-grade features, the AWK-1121/1127 series is the most compact dedicated WLAN client on the market. Smaller than a standard can of soda, it allows the space aboard AGVs to be efficiently utilized for other components.
The AWK-1121/1127 series complies with 802.11 a/b/g standards. It comes with Turbo Roaming™ to reduce handoff times within 100 meters, and is housed in a rugged, industrial-grade IP30-rated shell, giving it needed protection for industrial environments.
With the ioLogik E1200 and AWK-1121 installed on an AGV forklift, operators can be certain of steady and seamless control of their vehicles. This ensures a more responsive and efficient warehouse management system.
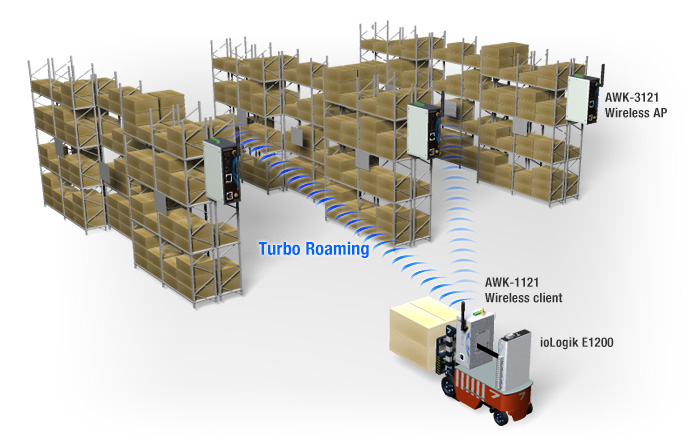
Case 4:Ethernet-based data acquisition in boiler control system
Factory automation technologies must monitor and control a myriad of information from numerous devices. In a plastics manufacturing environment, for example, the boiler control system is critical as it gathers and regulates information to ensure production is efficient and smooth. In this case study example, a Moxa customer combines eight sub-systems; power meters, water meters, displays, alarm output, and I/O status are controlled with the Modbus RTU interface. Due to greater distance between equipment, the Modbus TCP protocol is used for this application.
Due to excessive cost and the difficulty of a wired setup, data transmission via a wireless network is preferable. For this application, the setup of a stable and rugged wireless network is of critical importance.
Advantages of the Moxa Modbus system:
Modbus serial to Modbus TCP translation
Multiple slave/master support
Cascading Ethernet connections to save cost
Provides a stable wireless network
Responsive timeout feature which prevents the Modbus TCP section timeout
(due to an increased delay from the wireless link)
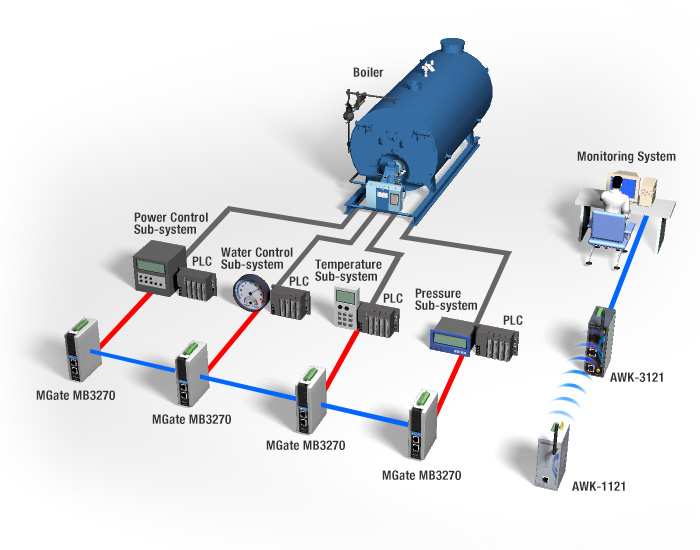 |