Resources / Case Studies
Taiwan
Cut Your Factory’s Idle Time by 70%
The journey from raw materials to finished products requires at least 70% of the total time to be spent on internal logistics, with products either being transported from station to station or sitting in storage for further processing. During this idle time, no production is taking place. To address this issue, a leading optoelectronics manufacturer in Taiwan introduced ECON's Automated Guided Vehicle (AGV) system to replace manual processes. The AGV system was integrated with the MES (Manufacturing Execution System) and WMS (Warehouse Management System) to achieve clearer visibility of logistics and production processes.
ECON discovered that wireless communications are key to helping AGVs move accurately in a factory. In most plants, there are multiple intersections, and T junctions are a critical zone for AGV management. ECON partnered with Moxa to build an ultra-reliable AGV wireless network to keep their AGVs always on the right move.
LEARN MORE
Summary
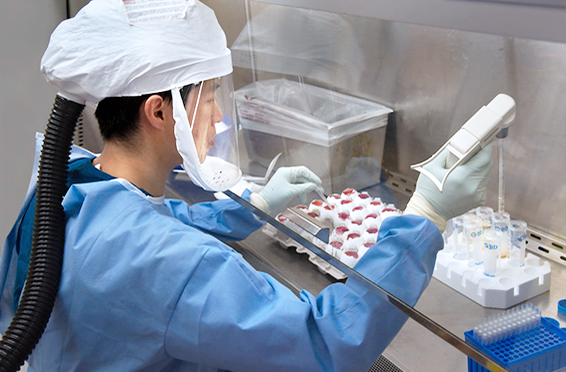
Challenges
- AGV system to replace manual processes, which were considered too time consuming and labor intensive.
- The complexity and diversity of AGV application scenarios makes it very difficult to find a set of powerful wireless network devices that are suitable for all scenarios.
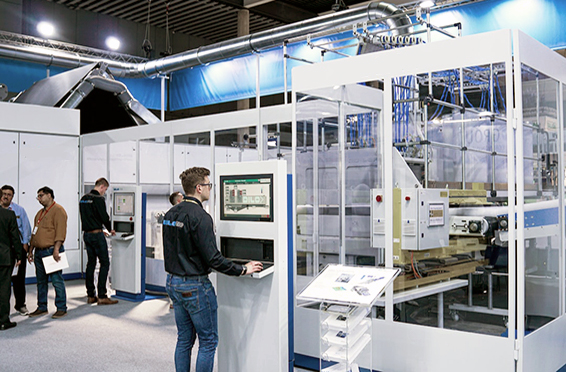
Solutions
- AGV path planning and design tools that are easy to use and do not require programming.
- Wireless communication technology that allows remote monitoring and scheduling of vehicles.
- Path maps on the cloud improve the scheduling flexibility.
Results
- True traceability: Integration of AGV, MES, WMS, and elevator systems.
- Labor saving: The cost of labor is reduced by 50% and the working efficiency is improved.
- Space saving: The areas used for temporary storage are no longer required, which means that the size of the site can be reduced by 20%.